NEW ONCOLOGY PLANT
The construction of our new oncology drug products plant is a major investment for injectable, liquid, and lyophilized products with more than 2000 square meters covered, three lyophilizers, three liquid filling lines, and research, development, and quality control laboratories under advanced technology and GMP standards. With the drug products manufactured we supply the domestic market and other countries opening more doors to the export of cutting-edge drug products for the industry. With more than 15 years of experience in oncology and the mission of being leaders, today our productive laboratory added the research and development of new molecules, which leads us to generate new jobs, and continue our growth.

BUILDING STRUCTURE AND PRODUCTION CAPACITY
The plant is located on the Panamericana Highway Km36.5 in the OKS Industrial Park, Garin, Province of Buenos Aires. We are 60 km from Ezeiza International Airport and 40 km from the Port of Buenos Aires. The production capacity for lyophilized oncology drug products is 80,000 units per month, while the production capacity for oncology drug products in liquid solutions is 150,000 units per month.
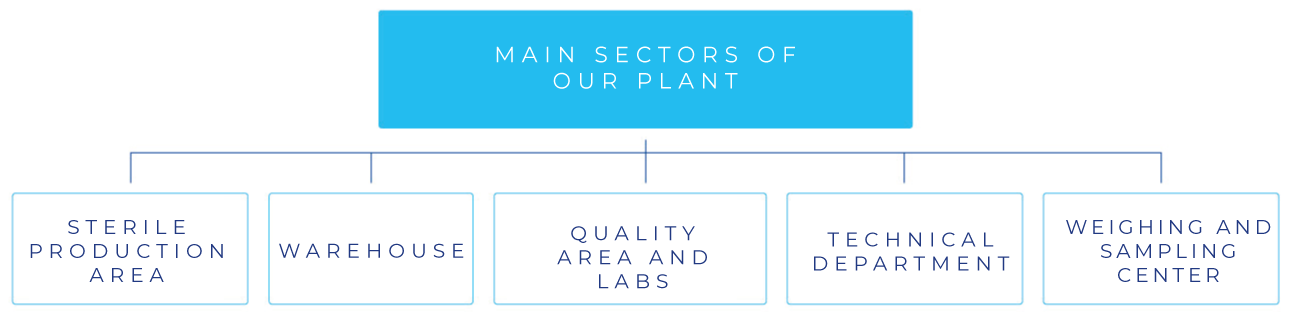
PLANT EQUIPMENT
The plant has central air handling units (UTAs/UMAs) that meet the highest quality requirements, with totally separate equipment to avoid any possibility of cross-contamination. The air quality for the sterile area meets the current ISO 14644 / GMP ANMAT requirements.
It has 3 lyophilizers, 2 of them have a condenser with an ice capacity of 45 kg and the other has a capacity of 55 Kg of ice. Each freeze dryer has 2 compressors. In case of failure of one compressor, the cycle is completed with the other compressor. The process control of the equipment has restricted access. It has an automatic and programmable system for cleaning in place with water for injection (CIP) and sterilization in place with pure steam (SIP) that allows the validation of these processes in the equipment. For CIP, it has a heated storage tank of 2000 l of water for injection. The sterilization is carried out directly with pure steam from the line and emits graphic records. The capping system of the vials is performed automatically inside the chamber after finishing the lyophilization cycle.
It has a non-viable particle counter equipment for each vial dosing line, three lines in total, which allows us to monitor and record the number of online particles of 0.5 and 5 microns size, generating a permanent report with qualified and validated software.
It has an integritest equipment to assure the integrity of the sterilizing membranes of the filter capsules before and after the filtration to assure the sterility of the dosage volume into the vials.
The water for injection and pure steam plant is composed of a reverse osmosis unit that pre-treats the drinking water. The generated water then feeds a distiller that simultaneously generates water for injection and pure steam.
The water for injection is stored in a 1500 l heated tank and is distributed with a sanitary pump in an AISI 316 L stainless steel loop. This entire design complies with current international and national sanitary standards.
The loop has a cooling system at the points of use that allows us to work during the manufacturing process of solutions at the desired temperature in a range between 0-80 °C. In all production areas, only water for injection is used for washing and rinsing materials.
The pure steam is distributed in a 316 L stainless steel pipe and it is used in the sterilization of lyophilizers, reactors and autoclaves.
To assure the absence of microorganisms coming from materials and devices to be used in every step of the aseptic process, they are sterilized in an autoclave with a double-door and an in-line pure steam. It complies with the qualifications and validations according to cGMP standards.
To assure the absence of bacterial endotoxins the vials to be used for the drug products are treated in an oven at high temperature with recirculated air filtered through HEPA filters. It complies with the qualifications and validations according to cGMP standards.
The washing machine, with a double water for injection and sterilized air cycle, guarantees the cleaning of the vials from 2 to 50 ml to be used for the drug products.
There are two semi-automatic liquid dosing machines for freeze-drying products and one for liquid products with peristaltic pumps and automatic pressing and closing systems for the rubber stopper. In the case of freeze-drying products, the closing of the vials with the rubber stopper is finished automatically inside the chamber of the lyophilizer at the end of the lyophilization cycle.
There are two electrical generators that supply the entire plant, avoiding unforeseen interruptions in the affiliate’s cycle and in the air and water systems.
The plant has areas for coding, optical checking, vials labeling, and final packaging with a system under GS1 standards that ensure the traceability of finished drug products, following a layout according to cGMP standards.